Burst Pipes Present Opportunities for Remediation Businesses
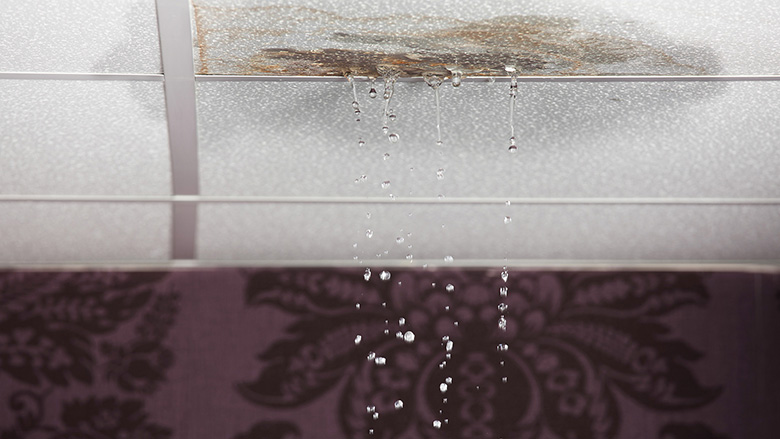
Photo: MediaProduction/E+ via Getty Images
Residential water damage in the US costs up to $20B annually, and burst pipes are a leading culprit. Often associated with freezing temperatures, pipes can burst at any time. Things like freezing temperatures, tree roots growing into pipes, rust, clogs, hard water, poor installation, and more are some of the lesser-known causes. But when pipes burst, no matter the cause, the damage can be severe. The average cost of damage from burst pipes is $27,000, a potentially devastating amount for uninsured homeowners and business owners and an unpleasant check to write for insurance companies.
In many parts of North America, freezing temperatures are an annual reality. Combine the inevitability of cold weather with aging infrastructure, and the result is a consistent story of water damage occurring. While this may be a bleak outlook for many, for restoration and abatement contractors, water damage is big business.
On the residential side of the restoration business, one in 60 insured homes filed a water damage claim from 2015 to 2020. And for commercial contractors, there has been a significant increase in high-dollar claims. Since 2015, water damage claims over $500,000 have doubled, and claims over $1M have tripled. In other words, the market is bursting with opportunity.
The importance of mold remediation training
While these numbers present tantalizing business opportunities, contractors cannot enter the space hastily. Mold from water damage presents serious health risks, and failing to remediate mold properly can have harmful consequences. Therefore, it’s critical to receive the proper education before attempting mold remediation. For those completely new to the industry, the Environmental Protection Agency (EPA) has an introductory course, but the gold standard certifications for remediation professionals come from the Institute of Inspection and Restoration Certification (IICRC), including the Applied Structural Drying certification and the Mold Remediation Specialist certification.
Steps of mold remediation
Certification courses will dive into the details of mold remediation for a variety of scenarios. However, here is an overview of the steps involved in mold remediation for burst pipes:
1. Cut off the flow of water
When a pipe bursts, the first step is to make sure it stops gushing water into the building. To limit the damage, start by turning off the water. Then, identify the source of the flooding and use a temporary measure to seal the pipe. While some people resort to clamps or rubber in an emergency, flexible seals generally work better. The pipes will need to be repaired or replaced by plumbing professionals eventually, but right after flooding begins, the priority is to limit the damage.
2. Contain the affected area
When pipes burst, mold’s best friend is abundant: moisture. Once moisture is present, mold can grow in 24-72 hours.
Fighting mold is a race against the clock. When pipes burst, mold’s best friend is abundant: moisture. Once moisture is present, mold can grow in 24-72 hours. For many, their first instinct is to dry the building as quickly as possible. But drying the building requires using powerful air movers which blow moisture off surfaces and into the air. If mold is present, it is blown into the air as well.
Without proper containment in place, the entire building can become part of the infected area as mold spores travel through the HVAC systems. Therefore, to avoid making a bad situation worse, contractors use containment walls to cordon off the impacted areas.
When it comes to containment, there are few options. For decades, erecting drywall walls to contain flooded areas was standard practice. Depending on the size of the affected area, constructing drywall containment walls can take 2-3 days, giving mold plenty of time to grow. These walls are not reusable, they’re labor-intensive to build and tear down, and they’re expensive for one-time use. These pitfalls inspired innovation: reusable, modular containment walls.
These walls, frequently made of aluminum, polycarbonate, or a combination of the two, quickly became popular in healthcare and other critical environments. As time has passed, they’ve spread into many other industries. During the pandemic, they exploded in popularity for patient isolation, showing their ability to keep harmful contaminants out, which is precisely what’s needed in mold remediation. Furthermore, they’re often designed to pair with negative air machines and portable HEPA vacuums, allowing for containment and filtration in one.
3. Stop mold growth
With containment and filtration in place, contractors can begin to safely dry the building. This involves two steps: blowing water off surfaces into the air with air movers and capturing the moisture in the air with dehumidifiers.
Depending on the extent of the flooding, contractors may daisy chain multiple air movers together to increase airflow and decrease drying time. Time is of the essence when drying a building to stop mold growth, so contractors need to have high-powered air movers on hand.
As the air movers blow moisture off surfaces and into the air, contractors use dehumidifiers to pull this moisture out of the air. By combining these tools, contractors remove not only the visible water but also the water that escapes the naked eye. This helps prevent further mold damage down the line from lingering moisture.
4. Eliminate mold
To keep any contaminated air from leaking out of the affected area, contractors must negatively pressurize the containment area. Negative air machines or portable air scrubbers are the go-to tools for this. This negative pressure directs airflow into the contained area rather than away from it.
If mold has grown inside the affected area, simply knocking mold off the surface won’t be enough. The mold will continue to grow, even if it can’t be seen, creating further problems down the road. Therefore, teams will often have to remove damaged drywall and other materials.
When removing these materials, mold spores and other harmful particulates can enter the air. To clean the air, contractors use HEPA portable air scrubbers, which remove 99.97% of particulates from the air. These machines draw air in, run it through filters, and then exhaust the filtered air outside the building through ductwork that fits seamlessly with the modular containment walls.
Mold, a moneymaker
Entering the mold remediation industry doesn’t happen overnight. It requires investment in training and the proper tools for the job. But as many industries face volatility, water damage isn’t going away. Where there is water damage, there will be mold, and where there is mold, there is an opportunity for those who understand what to do.
Looking for a reprint of this article?
From high-res PDFs to custom plaques, order your copy today!