Restoration Flashing Costs to Consider Part 2
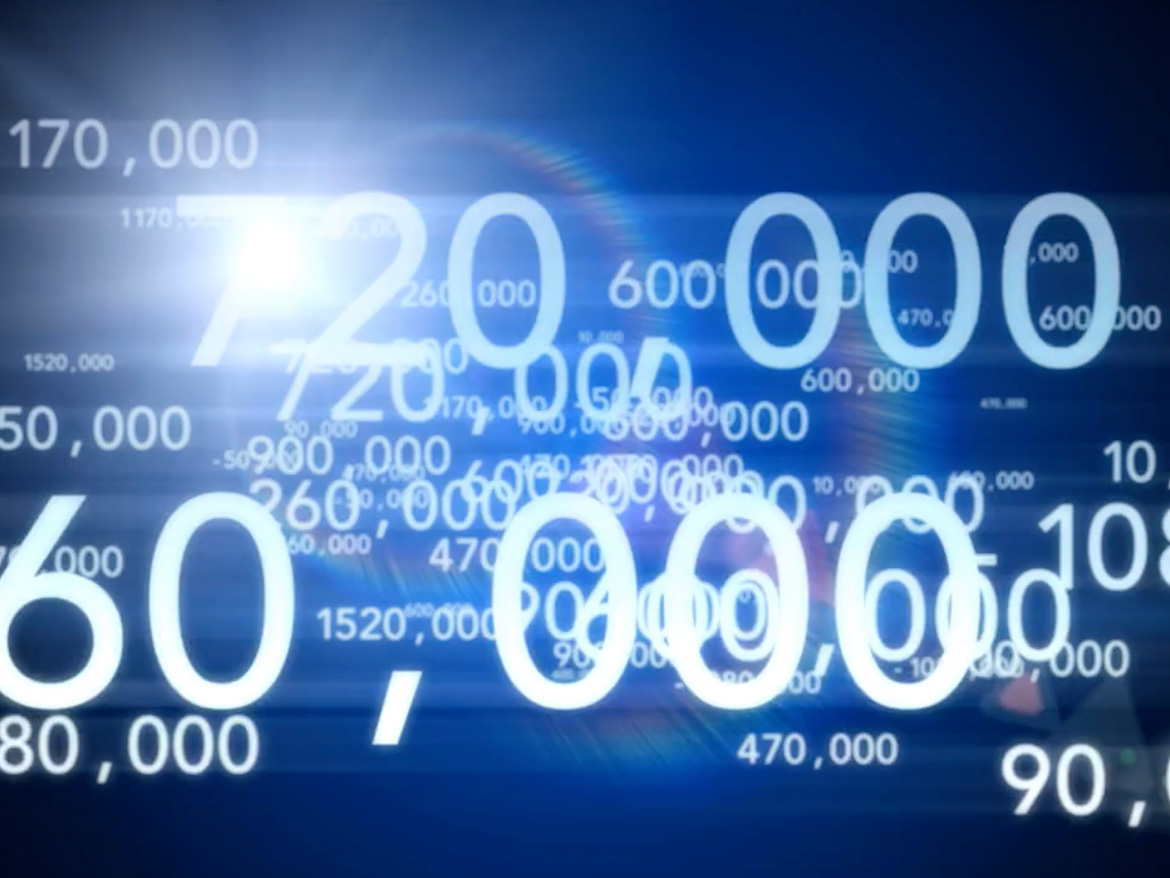
This article takes a four-foot masonry opening and breaks down the cost to properly flash the masonry opening versus random techniques performed by some estimators. This example references estimating against production changes to cover costs.
Estimating has many different methods. Restoration estimators are typically part commercial estimator, part restoration, and part magician. I have seen million-dollar jobs estimated and summarized on the back of an envelope and others on spreadsheets that NASA could not even follow. There is not just one type of restoration estimator, but we all have the same goal: understand cost, plan labor methods, and make money.
Whether you estimate on paper or digitally you need to have a system that allows you to see the entire concept of the structure you are estimating. Since a portion of restoration projects are performed without proper drawings, the estimator must assume many conditions, qualify, and estimate accordingly.
For me, I would flip through the pages when they existed and look at the plan, then the elevations, sections, and structural drawings, making notes before I ever recorded a measurement. I also always began on the plan of a drawing in the upper left-hand corner. There was no real reason, it just worked for me.
One of the tasks I had when estimating was windows, and since I am not one to “wing it,” I always measured and calculated my costs. I have learned many people in new construction have a cost in their head and they just go with it. I had one old employer tell me to take the perimeter of the two-story building and triple it, and that would give me a number he was happy with for flashing. Another boss would just change their brick production from 600 pieces per man/per day to 450 pieces per man/per day and figured that this would cover his costs.
Well, I am not one of those guys. I have to figure it down to the screws. Though I did not particularly like figuring windows and backing numbers out of my other quantities, it had to be done.
Here is an example: I have a 1:1 crew on a non-union project. Let's just say my brick layers (mechanics) are $30 per hour and helpers are $18 per hour. If I have a 28% burden, my day cost will be $492 per day without profit of equipment. If my production is 600 pieces per day for laying brick, my cost for a two-man crew is 82 cents per brick installed. If I drop production to 450 pieces per day my cost increases to $1.09 per brick installed. This estimating change allows for $1.09 per brick - $0.82 per brick = $0.27 per brick installed.
So, if you estimated your flashing by reducing the brick production, your 4-foot opening would be $40.50 per day for flashing materials overall ($0.27 per brick installed per day x 150 brick production difference), all with hoping that the production is actually made. This is an estimating mistake that the field cannot make up.
For example, if you had to flash one window 4 feet wide, you may have the following costs:
The overall cost is $ 43.90 per 4-foot opening for flashing (5 feet of flashing required for bearing). With this cost versus the production change, the project cannot afford to purchase the materials without becoming a loser.
It is important to estimate the cost of a specific task and really understand what tasks are involved so you can accurately bid a project, rather than just throw a number at it. Many can get away with throwing a number, but many cannot! I am one of those folks who cannot.
Once you really understand the cost of the flashing on a project, you can better evaluate the possibilities of alternate materials and the real cost differences. There are many products available for flashing a project in today’s market; take the time to understand an option before you decide if it is a savings or an additional expense to your project. Different membranes have different actual installation rates and performances as well as products that can properly adhere and seal them.
Here is an example: ethylene propylene diene monomer rubber (EPDM or tire tube material) is not compatible with a bituminous mastic (muck) because it causes it to bubble and stretch, and Thermoplastic Olefin (TPO) has a surface energy that will not bond to polyurethanes, silicones or polyethers. The list goes on. Today, since everything we use has a polymer modification of some sort, each manufacturer or membrane must be properly matched for a correct selection.
Flashing has become a critical component of the wall; if it fails, big money is spent to correct the problem. Estimating the costs correctly and choosing a cost-efficient method to begin with sure helps when putting a masonry budget together for the next project.
Looking for a reprint of this article?
From high-res PDFs to custom plaques, order your copy today!