Case Study
Prepping for Disaster: Hotel Escalator Fire
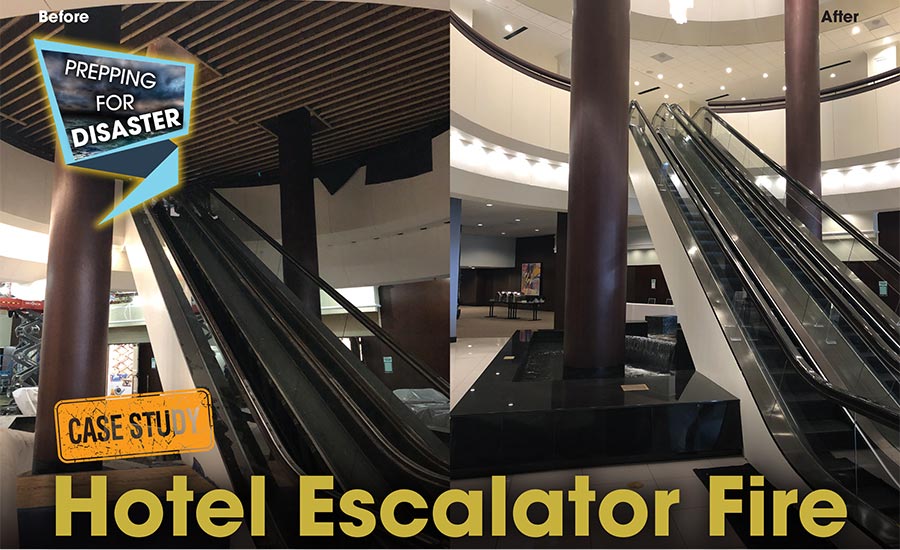
Photos courtesy of Burggraf Disaster Restoration
Editor’s Note:
In R&R, we love to tell YOUR stories of success! Do you have a cool case study to share? Email blevinsm@bnpmedia.com!
Tell us a little bit about your company.
Burggraf Disaster Restoration is a full-service restoration company in Tulsa, Okla. We’re highly experienced in emergency response and disaster. We focus on coordinating the immediate response measures and taking the necessary measures to prevent secondary damage. Over the past 31 years in the disaster restoration industry, we have built a quality team. We also invest in the latest high-tech equipment so our team is more efficient, thereby speeding up the process of putting you back in business. And getting back to business will obviously be your biggest concern.
2. We heard you tackled a loss at a hotel. Give us the details! Was this a client you’ve worked with in the past or already had a relationship with?
We are allied members of an elite group of hoteliers in our region called the Metro Tulsa Hotel & Lodging Association (MTH&LA) and we hold a position on their board of directors as well. The president of this association is the general manager of one of the largest hotels in Oklahoma. We have provided service for this particular hotel in the past and developed a relationship with the management, so when this event happened, they didn’t hesitate to call us.
3. How did you land/sell the job?
We specialize in commercial losses and we shine when it comes to disaster planning with our clients on large loss situations. We have developed a one-of-a-kind Emergency Response Plan that we provide to our commercial clients. This ERP is a tool that helps guide our clients so they are well-prepared to handle a disaster when they occur. We personalize the program to benefit our clients’ needs. We had an ERP in place with this customer when the loss happened and it minimized the stress and reduced their recovery time.
4. When did the loss happen? How soon after were you called in?
Right before Thanksgiving last year, we were finishing up a very challenging water loss they had when the assistant general manager called and began to describe a fire they had that day in their escalator. They needed our assistance immediately to take care of it.
All guests of the hotel and the hotel staff had to be evacuated due to the large amount of smoke. When we arrived, the fire department was still assessing the building and would not allow anyone in the property until they gave the all clear.
The assistant GM introduced me to the captain in charge at that time, and he asked for our assistance in removing the smoke from the building by installing some of our commercial air filtration devices and directing the air to exit the building until they could clear the building. We are always willing to assist the first responders in any way we can and we began mobilizing our equipment to the property immediately.
5. How many people did you have working the loss?
With our staff and the numerous subcontractors we had performing specialized tasks, there would be anywhere between 200 to 350 people, depending on the day. Some days we would require our subcontractors to double or triple their staff in order to manage a requirement needed on short notice.
Part of being successful at disaster planning is having the knowledge to manage an ever-evolving schedule and being able to think outside the box when needed. A lot of this planning is knowing where to put staff and when you need to add to, or sometimes take away from, your staff on a minute’s notice.
6. What was the scope of work?
Once the fire department gave us the all clear to enter, we started our assessment of the property. This is one of the largest hotels in the state--some 484 rooms--so as you can imagine, the assessment of the damage took several weeks to compile, even with the assistance of a network of professionals from our company as well as the insurance carrier, multiple consultants, and an industrial hygienist.
We all teamed up to generate a scope of the damage and develop a disaster plan that would be most beneficial for our customers. The industrial hygienist evaluated the air quality in the structure and determined that the building was uninhabitable until all the ductwork was cleaned, retested, and passed for acceptable air quality.
In a nutshell, the scope of work we developed with the assessment team consisted of cleaning all the ductwork throughout the entire property from the ground floor to the fifteenth floor. This also involved cleaning every square inch of the building and contents along the way so we did not have cross-contamination.
7. What kind of equipment did you use for the remediation process? Did you have all the equipment did you need, or did you rent some?
On a job of this size, it takes a considerable amount of equipment. The equipment included everything from 47 different sizes of ladders to special articulating boom lifts and pallets of cleaning supplies. Fortunately for us, we have one of the largest equipment fleets in the state of Oklahoma, which gave us the opportunity to supply the majority of the equipment without renting it.
Initially, we had 57 extra large air scrubbers to control the odor in the hotel, a multitude of personal protection equipment (i.e., Tyvek suits, gloves, hardhats, dust masks, etc.), a large amount of HEPA vacuums for cleaning, 18 sections of scaffolding, and 26 scissor lifts. We did rent most of the scissor lifts, but supplied the remaining equipment and tools necessary to complete the job.
Since we had to clean the ductwork throughout the whole building, we had the HVAC system shut down in the middle of winter, so we had to control the environment to prevent the structure from internal freezing. We own three large 750,000 BTU heaters and we had all three on site, pumping a total of 2,250,000 BTUs of heat into the building for a couple of months. We also supplied the generators to run this equipment.
8. Did the business stay open during restoration? Or if not, were they able to open back up sooner thanks to some of your processes?
Upon receipt of the environmental report, the decision was made to close the hotel down until an acceptable air quality clearance report could be provided to the owners of the hotel. We had the hotel shut down for 73 days during the process of performing a caustic cleaning. There was roughly 12 months’ worth of work performed during this 73-day period at all levels, from cleaning to bringing the whole building’s fire suppression system and electrical systems up to current code.
9. What was the most difficult part of this job, and how did you overcome it?
The time constraint was the most difficult part. There wasn’t any additional time built into the schedule for errors, and there were unforeseen elements that would arise every day that had to be dealt with and would change the scheduling. With all the activity going on and new damage discovered daily, the job progress would change frequently. The daily progress meetings with owners, management and staff supervisors was a constant moving target.
Another area that was very challenging was rebuilding the HVAC duct components that were damaged from the smoke and soot. There are internal boxes, which are called VAV boxes (variable air volume) and fan-powered boxes, with dampers and motors that control the amount of air flow going through the duct system. Electronic controllers on each box communicate with the maintenance department’s computers.
After assessing all 36 VAV boxes and 18 fan-powered boxes, it was determined they had to be replaced. Each unit, which ranged in size from a desk to half the size of a small car, had to be special ordered.
After being informed that there would be a considerable amount of lead time (time that we didn’t have) waiting for the units to arrive, we had to come up with a plan B. We built new boxes compatible with the voltage requirements and additional specs required to perform at the capacity needed. This was all part of the process of turning over a clean environment upon completion and passing the air quality inspection.
If it weren’t for the collaboration and quick thinking of our management staff coming together with owners and management of our contractors, this would not have happened.
10. What was the biggest victory from this job?
The biggest victory was completing one of the largest fire losses in our region for 2019 in the amount of time allotted. Everyone was anticipating that it would not be done, but we pulled together as a company and performed every day.
I want to thank all of our staff, from clerical to project management to the owners. If it were not for them, this project would not have been successful!
Looking for a reprint of this article?
From high-res PDFs to custom plaques, order your copy today!