Restoring Success: Inventory Management & Controlling What's Out of Control
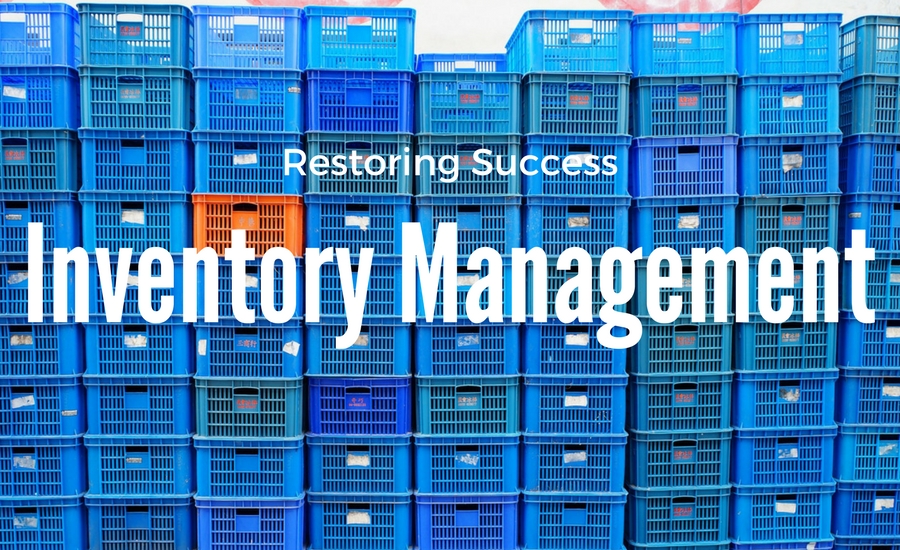
The warehouse is a mess! A customer called to tell you an air mover was left on-site. Somebody left the company and nobody retrieved the meter assigned to the person.
A universal challenge in our industry is inventory management. In 2014, I presented this topic in the context of evaluating your needs and employing the right methods and resources.
Fast forward to today, there are more potential solutions than ever on the market to provide operational support to effectively managing our tools and equipment. It is more common today than ever before to have additional tracking needs for items like tablets and iPads. The dollar value of a restoration company’s investment in tools and equipment is typically in the top investment areas along with vehicles, facilities and staff. These assets are also critical to our ability to produce revenue and serve our customers.
It is both wise and natural to have a desire to optimize our resources and effectively manage our inventories. Managing our inventory includes but it not limited:
- Location and possession: Where is it now? Who has it? Where does it belong?
- Aggregate: Information regarding quantities of specific items, ages, in-service, and/or out of service.
- Detailed information and maintenance records: Date purchased, serial numbers, maintenance records, etc.
- Tools and reports: To assist you in keeping everything in optimal and efficient working order.
At any given point, it can be a bit overwhelming to either employ a system or improve an existing system. Once you commit to a system, the following checklist will assist you in effectively implementing and maintaining the system.
Design your space and establish locations
This critical first step is imperative to ensuring that everything is where it belongs. No matter how big or small your spaces, they must be organized, designed, and defined. As an example, consider a specific dehumidifier: where does it belong when it is not on a job? To keep things organized, there must be a specific designated location for things when not being employed in the field: A specific truck, A specific spot in the warehouse, etc. There are a variety of approaches to this and different levels of details but the end result should be a location that can be assigned to an individual inventory item.
Examples:
- Truck 10, Shelf 1
- Bin 1, Shelf 2
Plan Resources
Purchasing and or adopting a new system is the first step but there is going to be an investment of time and resources that should be planned for in the investment. The amount of resources you will need to invest will vary based on your existing systems and information as well as the size of your inventory. Allow and plan resources for the following:
- A point person that will lead and manage the implementation process.
- Location design and defining.
- Initial equipment logging and coding. Whether you create your own system or use a barcode, or QR, someone will have to physically assign and label each inventory item and record all appropriate data for the initial inventory.
- Software installation, training and troubleshooting.
- Define processes, procedures, and accountabilities
Initial Inventory Process
Everything is on the move as you establish or set up the initial inventory. Think through the process to make it efficient and effective.
- Label/code location. For example, it should be on the same spot on every air mover.
- Plan for multiples items within a unit. For example, if you have a meter kit with multiple meters, you may want to allow the kit to be an individual item and the individual meters to have their own unique inventory item and be related to the kit. This will accommodate the needs of all these items’ movement and records while also allowing for efficient movement of the kit as a whole.
Processes and Procedures
It will be necessary to layout processes and procedures to maintain the system. A variety of events will need to be accounted for in addition to daily movement and operations. Clear expectations must be defined. Individual staff members must be designated for being responsible for certain action items. Accountabilities for non-compliance of process must be in place. Things to consider:
- Adding New Inventory Item and/or Removing/Disposal of Inventory Item
- Assigning and approving items assigned to individuals/and or vehicles
- New team members/Exiting team members
- Out for service
Improving your existing inventory management system is a good investment but must be approached deliberately. It may be tempting to take some short cuts but a well-designed and most importantly a well implemented system may reap great reward.
Looking for a reprint of this article?
From high-res PDFs to custom plaques, order your copy today!