3 Ways You Can Make Better Use of Energy in Drying
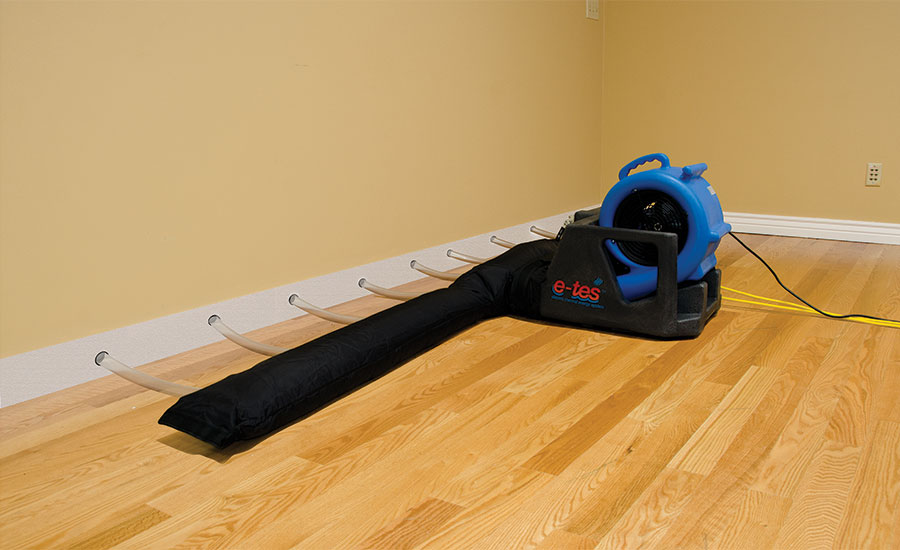
High heat drying. Cooking the house. Baking the moisture out. These descriptions all tend to create a fear of the subject of using energy in drying. The fact is that we use energy application in drying every structure that we dry. Unfortunately as a result of overuse or perhaps due to a lack of understanding, heat has been misused as indicated by the first descriptions.
The fact is that an exchange of energy is required for water molecules to go through a phase change. Let’s just say that you have a lot of ice. Perhaps you were in Boston during the record snow storms this winter. The first approach was to shovel and plow the snow out of the way. Unfortunately there was so much snow that eventually there was nowhere to put it. Besides wanting that blasted snow to quit falling, what did Boston need to get rid of all of that snow? They needed some heat energy! When the temperature rose above freezing all that snow started to melt. That’s the phase change from ice to liquid.
Now in a water damage situation, we are in the same position as the people of Boston. We have a lot of water in the liquid phase inside a structure and we need to get rid of it. The first step is to extract as much of the bulk water as possible. Unfortunately though, we can’t get all of the moisture just through extracting. Evaporation is our next tool. It gets the water left behind into the air as vapor so that we can remove it with dehumidifiers or ventilation. Just like the snow in Boston needed heat to melt, the liquid in our environment needs energy to go through the phase change from liquid to vapor known as evaporation. The more quickly we can get energy into the water, the faster evaporation will occur and the faster we remove excess water from the structural materials.
Look at a few of the basic tools that each restorer has at their disposal: installed HVAC units, air movers, dehumidifiers, auxiliary heating devices. Each of them helps the restorer to deliver or manage energy. So how can you make better use of the tools that you already have to utilize energy in drying?
1. Installed HVAC Units and Air Movers
Despite the persistent battle regarding the use or reduction in the use of air movers surrounding the S500, air movers still play a critical role in drying. Their role has not changed. Air movers are critical to the success of any project. Why?
This is a question that I ask in every class that I teach. Why do we use air movers? I receive a variety of answers that range from speeding drying, to sweeping away evaporating moisture from wet surfaces to reducing the pressure over the wet surface. While there may be some truth to each of these answers, they are not the primary reason why we use rapid air movement in drying.
Air movement speeds energy transfer. When air flow is warmer than the surfaces it is moving across, energy is imparted from the air to that surface. The faster the air is moving the more readily it transfers energy. When air flow is cooler than the surface it is moving across, energy is lost from that surface to the air. Therefore, air movers are being used as energy transfer devices.
To best utilize air movers in water restoration, warm the drying environment. A warmer drying environment has more energy available to transfer to the wet surfaces. So use the building’s installed HVAC to warm the drying environment when possible. Try to get ambient air to around 90?F using the installed HVAC. Obviously sometimes the customer isn’t going to allow that, so agree with them on the warmest possible drying environment so that you get what energy you can from the HVAC. By warming the air and utilizing high-speed air flow you transfer more energy faster into the wet surfaces. This speeds evaporation and therefore moisture removal.
2. Dehumidifers
Whether using LGR’s, standard refrigerant dehumidifiers or desiccant dehumidifiers, each introduces energy to the environment it is installed in. One way to make better use of the energy from these units is to install containment around the drying chambers that you are working in to make them as small as reasonably possible. This helps to consolidate that energy and allow it to build. That energy can then be put to work drying the materials in that environment by utilizing rapid airflow. When combined with the energy from installed HVAC units you will have a winning combination.
Another way to utilize the energy that dehumidifiers put off is when drying hard surface floor coverings such as hardwood or tile. When combining contained dehumidifier process air with vacuum and mat systems the energy available makes drying these materials substantially more effective.
In order to concentrate the energy to the wet surface, plastic containment is installed over the floor and floated with the output of the unit. Dehumidifiers that have a convenient attachment location for the lay flat ducting make floating the containment very simple. Just attach a short piece of lay flat ducting to the outlet and run that under the edge of the containment. This delivers the energy from your dehumidifier directly to the water that you are removing from these materials.
3. Auxiliary Heat Devices
There are different types of heating devices available to the restorer and each has specific application techniques. The two primary types are ambient heat units and directed heat units. As the name implies, ambient heat units are designed to heat the ambient air of the entire structure or drying chamber. Directed heat units are designed to make direct application of heat to the wet surfaces. Since both of these units are designed to deliver more energy than a dehumidifier, proper application of them is important.
Ambient heat units are most common. These can range from a small electric heating unit to a fuel powered unit that delivers hundreds of thousands, if not millions, of BTU’s. Since they must heat larger volumes of air these units tend to have higher BTU outputs than that of directed heat units. These must be combined with significant air movement and caution should be taken to examine the temperatures of dry materials near the ceiling of the drying environment. Even though these materials are dry, they do contain critical moisture in the vapor phase that is removed quite rapidly by high heat. Over drying of these materials that were never affected can create damage like cracking and separation.
Even though ambient heating units can deliver enough heat to raise ambient temperatures well over 100ºF, this is not recommended. When using these heat units usually ambient temperatures of 95ºF are sufficient to create adequate drying conditions. Avoid the temptation to “cook the house.” You probably won’t like what you get.
Directed heat units are designed with comparably lower heat output. This is because the techniques they are made for are heating relatively smaller quantities of air using containment directly to the wet surface. Due to this type of containment it also tends to be easier to control the effect of the addition of energy to the drying environment. Also, since you are heating ambient air and applying it directly to the surface, ambient temperatures of 95ºF yield surface temperatures of approximately 110ºF.
Using these units to float carpet to deliver heat to the subfloor and base of the walls is very effective. These directed heat units are also what has motivated the return to using dehumidifiers to float plastic containment over hard surface floors. The same floor drying procedure noted above with dehumidifiers can be employed with directed heat units. Simply float containment over a hardwood floor with the directed heat unit and combine that with the use of a vacuum mat system to remove the moisture. Never attempt to dry a hardwood floor without the use of a properly installed vacuum mat hardwood floor drying system.
Directed heat systems can also be used to dry difficult to dry areas much in the same way you might use a hair dryer. Simply point the directed heat unit at the wet area of concern and add energy to get the moisture to move.
Three ways to make better use of energy in drying include:
- Utilize the installed HVAC to warm the air in the drying environment to approximately 90ºF and use air movers to transfer that energy into the water.
- Make better use of containment to concentrate the energy coming off of the dehumidifier.
- Either use ambient heating units to heat the environment to around 95ºF and rapid air movement to transfer the energy or use directed heat drying equipment to directly apply heat to wet materials with ambient temperatures at approximately 95ºF.
So there is no reason to cook the house, overheat the structure or any number of other unmentionable misuses of energy in drying. Utilize the three simple suggestions here to confidently make better use of energy. To become more adept at making use of energy in drying seek out training options that will teach you proven techniques for utilizing energy properly.
Looking for a reprint of this article?
From high-res PDFs to custom plaques, order your copy today!